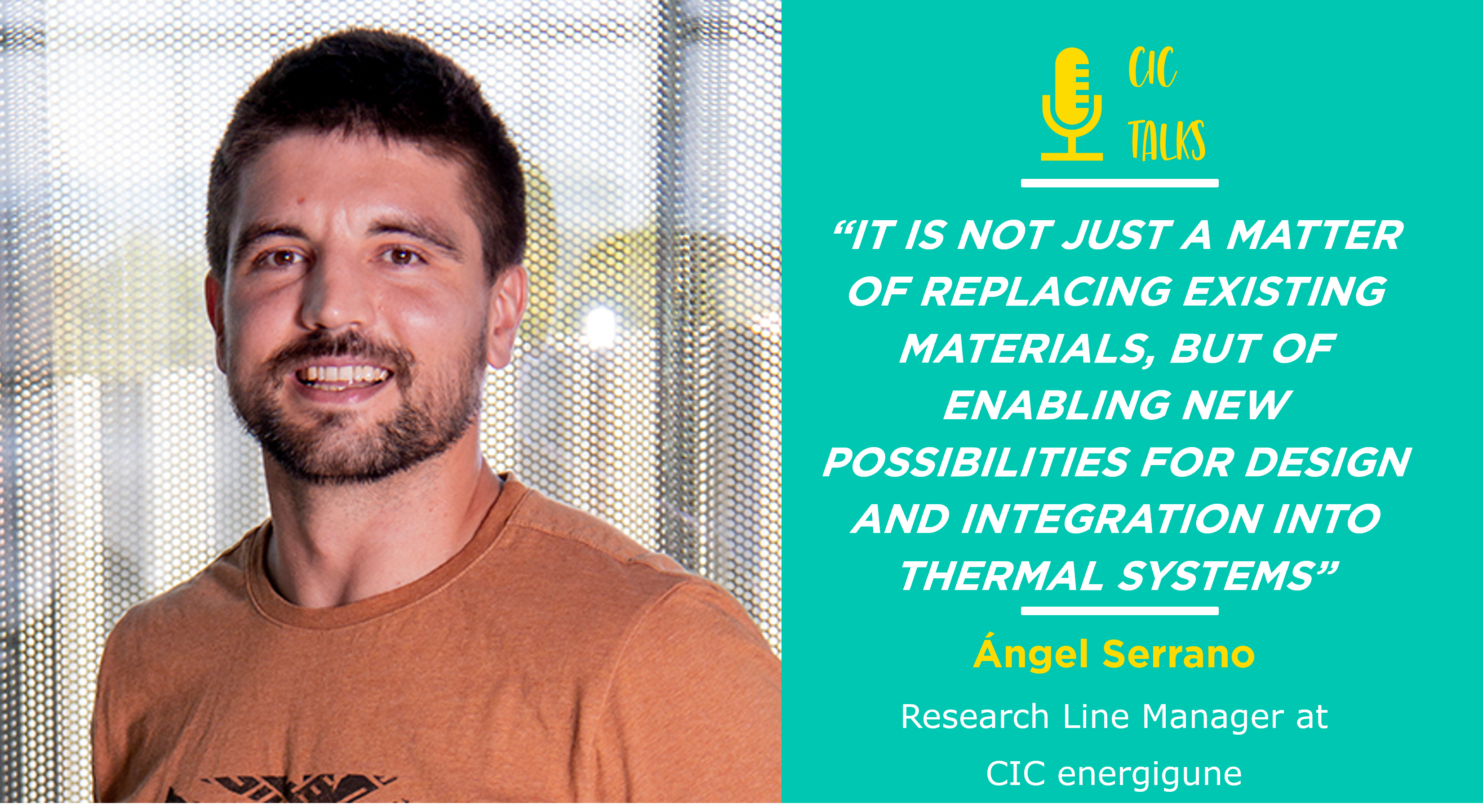
1. What role do PCMs play in the energy transition today, and what limitations do conventional materials present?
Phase Change Materials (PCMs) play a key role in thermal energy storage, as they can store and release large amounts of energy within a small volume and at nearly constant temperatures. They are especially useful in applications that require managing demand peaks, stabilizing temperatures, or improving the energy efficiency of thermal systems.
However, traditional PCMs face several challenges to varying degrees, such as subcooling, phase segregation, limited thermal and cycling stability, and relatively high costs. Furthermore, there are temperature ranges in which available options are particularly scarce. Although multiple strategies have been developed over the years to mitigate these limitations, achieving significant improvements in PCM performance requires exploring alternative phase transitions and designing new chemical compositions with enhanced properties.
2. CIC energiGUNE has committed to the development of solid-state PCMs. What exactly does working with solid-solid materials involve, and why is this such a unique research line?
Most PCMs undergo a solid-to-liquid phase change, which can lead to issues like leakage, deformation, or the need for containment systems. In contrast, solid-solid PCMs retain their shape since the change occurs within their crystalline structure. This improves safety and allows for simpler system designs, such as eliminating the need for a heat exchanger.
Despite their advantages, solid-solid PCMs are uncommon. While some materials exhibit solid-solid transitions, achieving these transitions with sufficient energy and at the right temperature is not trivial. Moreover, designing them properly requires a deep understanding of how their transition works and how to tune it through their chemical structure. At CIC energiGUNE, we have been developing this line for years, positioning ourselves as one of the few centers in Europe specialized in solid-solid PCMs. Our expertise enables us to identify, synthesize, and characterize these materials with real-world applicability in mind.
3. What are the main technical barriers to working with solid-solid PCMs, and how has your group addressed them?
One of the major challenges is the low transition enthalpy typically found in these materials. To be competitive, we need to maximize energy density without compromising thermal stability or cycling repeatability. In addition, characterizing these transitions and understanding them is key to unlocking their full potential.
Our group works with advanced techniques such as temperature-variable calorimetry, X-ray diffraction, and spectroscopy to track structural transitions in detail. We also use simulation tools to predict structures and optimize compositions before synthesis. This integrated approach allows us to overcome classical development barriers and bring these materials closer to real-world application.
4. In what types of applications can these innovative, tailor-made solid-solid PCMs make a difference?
The advantages are clear in applications where space, reliability, or sensitivity to temperature changes are critical. They are especially useful in sectors such as food, pharmaceuticals, or chemicals, where thermal gradients are small and space constraints are crucial. Solid-solid PCMs enable efficient integration of thermal storage into existing facilities.
They are also promising in fields like power electronics, aviation, electric mobility, or portable devices, where every gram and centimeter matter.
Additionally, the ability to design materials to measure allows tuning the transition temperature to the optimal range for each application—something not easily achievable with commercial materials. The key is to see the PCM not just as an energy storage medium but as a multifunctional material that adapts to the environment in which it will be integrated.
5. From your experience, what is needed for these disruptive solutions to reach the market?
Technology transfer requires overcoming several steps: from validation under real conditions to scaling up the synthesis process. We collaborate with companies to tailor the materials to their specific needs, integrate them into prototypes, and validate performance under actual operating conditions.
It is essential to demonstrate long-term stability, competitive costs, and compatibility with industrial processes. But it´s also necessary to shift the mindset: it´s not just about replacing existing materials, but about enabling new possibilities for design and integration in thermal systems.
6. Plastic crystals are one of your most established research lines. What advantages do they offer compared to other PCMs, and why do they continue to represent a unique opportunity?
Plastic crystals are a type of solid-solid PCM whose high energy density is based on the internal formation and breaking of strong hydrogen bonds. Most interestingly, some of these compounds exhibit thermal transitions in the 120°C to 250°C range, a temperature window where traditional PCMs face stability issues or simply do not operate. This opens up opportunities in sectors such as industrial thermal storage, solar thermal generation, or medium-temperature process integration.
At CIC energiGUNE, we are working to exploit the full potential of plastic crystals, addressing not only material-level optimization but also key challenges for real use, such as processability, system integration, and validation under relevant operating conditions. This line of work is not only scientifically innovative but also aligns closely with many European calls focused on industrial energy efficiency and decarbonization.
7. What is the future outlook in this field? What can we expect from CIC energiGUNE in the coming years?
Thermal energy storage will be key to the energy transition, especially in industrial sectors and hybrid systems where heat management is critical. At CIC energiGUNE, we will continue to strengthen our solid-solid PCM line, where effective solutions are still scarce.
These materials open new opportunities in industrial applications, solar thermal energy, or waste heat recovery. Our goal is clear: to design disruptive materials that expand the limits of thermal storage and contribute to real decarbonization—starting at the material level.
If you want to know the latest trends in energy storage and new developments in research, subscribe.
If you want to join a top-level team, collaborate with specialists in multiple disciplines or tell us about your concerns, don't think twice...