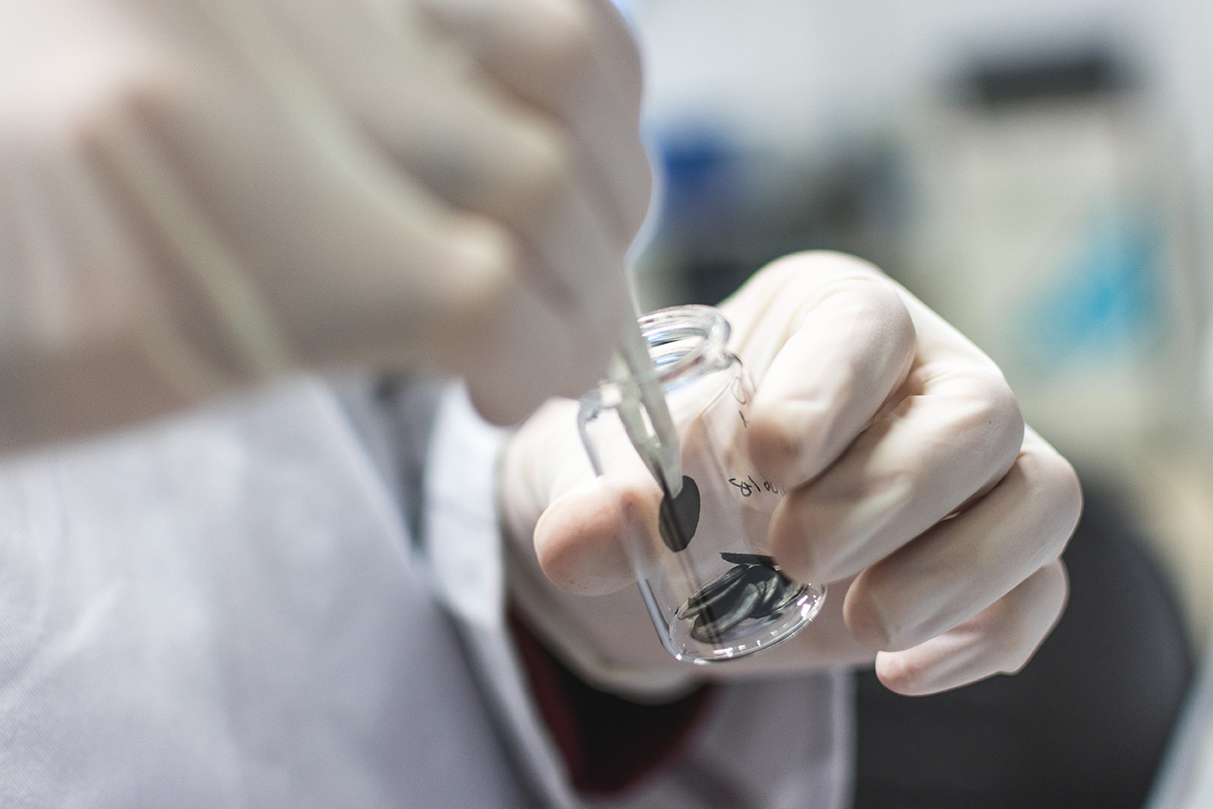
Li-ion batteries have reached a dominant position in the consumer electronics, power tools and electromobility sectors. Even stationary storage is looking at lithium-ion as technology of choice. However, the continuous demand for better performance, full safety and lower cost is pushing lithium-ion batteries towards its limits.
Following pioneer work on alkali metal intercalation on Prussian-blue materials by M. Armand and co-workers, the first rechargeable Li-ion battery reported in 1976 by S. Whittingham relied on TiS2 as positive electrode, lithium metal as negative electrode and a liquid electrolyte based on dimetoxyethane and tetrahydrofuran as organic solvents and LiClO4 as lithium-ion conductive salt.
However, this cell presented two important problems that prevented commercialisation at the time: 1) low energy density nested on the low cell voltage (<2.5 V), and 2) serious safety hazards originated by lithium dendrite growth that caused internal short circuit.
The investigations led by Goodenough in the 80s solved the energy density problem by developing three families of positive electrode materials: 1) layered oxides, LiCoO2 delivering a cell voltage ~4 V; 2) spinel oxides, LiMn2O4, with cell voltages in the 3 to 4 V range; 3) polyanions, LixFe2(SO4)3 which can exceed by one volt the cell voltage of transition metal dichalcogenides.
Even if the energy density problem had been addressed with the three families of positive electrode materials, the lithium dendrite growth problem was still present.
In parallel to the development of new cathode materials, the intercalation of lithium on Li-free anodes such as graphite using propylene carbonate (PC) based electrolytes had been pursued with no success. In 1990, J. Dahn and collaborators obtained reversible lithium intercalation on graphite using ethylene carbonate (EC) as electrolyte co-solvent.
In 1991, inspired by all investigations carried out to date, Sony commercialised the first rechargeable Li-ion battery based on a LiCoO2 cathode, hard carbon anode and PC-based electrolyte. After this, EC and dimethyl carbonate (DMC) co-solvents, as well as graphite negative electrodes in 1994, were progressively introduced providing stability up to 4 V. Since then, the majority of Li-ion batteries are still based on graphite as negative electrode material.
In contrast, the number positive electrode materials has increased. The need to remove Co, due to environmental and economic reasons, in the first family of layered cathode materials resulted in development of LiNi1–y–zMnyCozO2 (NMC) and LiNi1-y-zCoyAlzO2 (NCA) which, nowadays, are the dominant positive electrode materials owing to their high specific capacity.
As for the other two cathode families, the spinel one evolved through partial Ni-Mn substitutions resulting in the high voltage cathode material LiMn1.5Ni0.5O4 (4.7 V) which, despite the promise of high energy density, still lacks of a stable electrolyte that allows operation at those voltages.
Meanwhile, the exploration of polyanionic materials, third family of positive electrode materials, resulted in olivine LiFePO4 which despite its low operating voltage ~3.2 V delivers excellent cycling efficiency with long life span and thermal stability. Particularly, after Armand’s idea of coating the iron phosphate with carbon.
The figure below shows a schematic summary of Li-ion battery development in terms of the three positive electrode families that have reached the commercial stage.
Still, further improvements are demanded from current applications in terms of energy density, lower cost, life span and safety.
Considering that graphite has a higher specific capacity than any insertion cathode up to date, the development of new positive electrode materials with increased specific capacity would have a remarkable impact on the energy density.
Regarding the three main cathode families presented previously, further developments can be explored in the short term, namely lithium-rich compositions of layered oxides such as Li1.2Mn0.6Ni0.2O2 or NMC-based materials with lower Co content and/or inert ion doping which tends to stabilize the crystalline structure of these materials.
The consolidation of high voltage spinel as positive electrode depends on the discovery of a suitable electrolyte that can withstand operation above 5 V; here, novel solid electrolytes (ceramics and glass ceramics) and advanced liquid electrolytes (ionic liquids) can be the key component that enable high voltage Li-ion batteries. In general, integration of solid electrolytes and suitable mass production processing techniques will trigger the advent of the intensively searched solid state batteries.
In terms of anodes, graphite has several drawbacks being the most important one the limited rate capability upon lithiation which means limited battery charging speed followed by first cycle irreversible capacity. Li4Ti5O12 anode material solved these problems but it only has ~50% the specific capacity of graphite. Currently, Si or SiOx incorporation in graphite is a solution being explored.
In the mid- and long-term, the search for advanced materials shall be open to positive and negative electrodes and electrolytes, as well as to new chemistries. Known candidates based on intercalation chemistry would be Na-ion, Mg-ion and K-ion. In this case, the development of materials can be addressed on the basis of Li-ion analogue materials.
Beyond intercalation chemistry, new mechanisms based on conversion or displacement reactions with very high storage capacity can open a whole new set of application possibilities. Among these chemistries, Li-metal, Li-S and Li-O2 batteries are the most known and mainly relay on the development of advanced materials for lithium metal stabilization.
Batteries based on conversion reaction electroactive materials are also a promising alternative that can deliver very high energy density. However, advanced materials for this technology will have to overcome the degradation and the voltage hysteresis consistently observed throughout the last years.
As it happens, Li-ion technology has been developed over three cathode families and two anodes. Despite constant improvements are achieved in terms of electrochemical performance of Li-ion batteries, we are close to the limit of the technology. New families of materials are needed to keep the momentum of batteries, Li-ion or others, and cover all needs ahead.
If you want to know the latest trends in energy storage and new developments in research, subscribe.
If you want to join a top-level team, collaborate with specialists in multiple disciplines or tell us about your concerns, don't think twice...